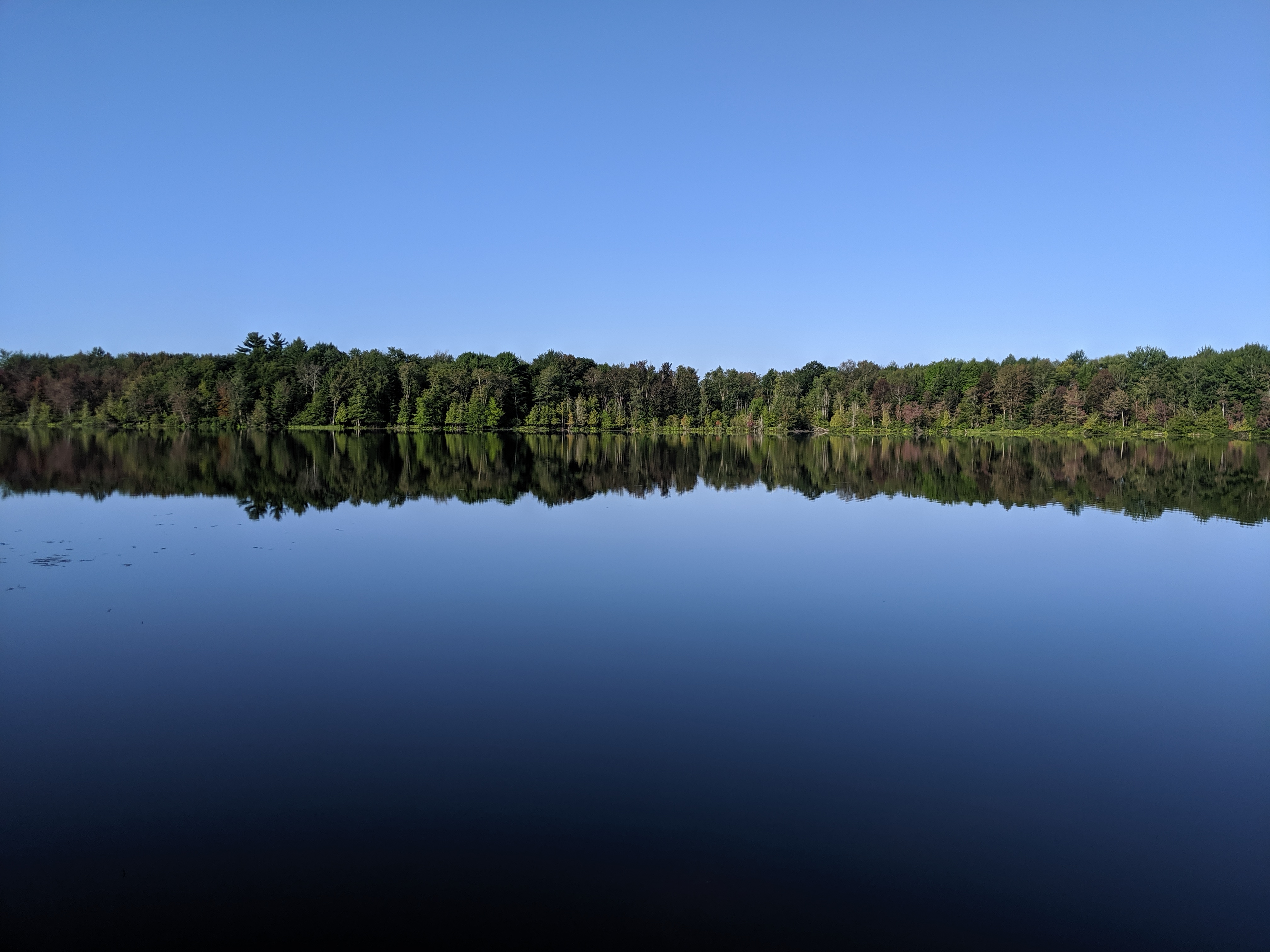
How Leveraging Contract Manufacturing For Foreign Company Can Save Your Fixed Capital Investment
In an increasingly competitive global marketplace, foreign companies are constantly seeking innovative strategies to optimise their operations and maximise cost efficiency. One such strategy that has gained traction in recent years is leveraging contract manufacturing. By outsourcing production to specialised manufacturers, foreign companies can significantly reduce their fixed capital investment, mitigate risks, and enhance flexibility in their supply chain management.
Here’s how contract manufacturing can help you save your fixed capital investment:
1. Minimizing Capital Expenditure
Setting up manufacturing facilities involves significant capital outlay, including investments in land, infrastructure, machinery, and technology. These initial expenses can be prohibitive, particularly for foreign companies entering new markets. By partnering with contract manufacturers, these companies can sidestep these hefty upfront costs. Instead, they can allocate their financial resources towards core business activities such as research and development, marketing, and expanding into new markets. This strategic reallocation not only conserves capital but also drives innovation and growth, enabling businesses to focus on areas that directly contribute to their competitive advantage.
2. Reducing Operational Costs
Beyond the initial capital expenditure, operating a manufacturing facility entails ongoing overhead expenses. These include utilities, maintenance, labor, and regulatory compliance. Managing these operational costs can be a significant financial burden, especially in foreign markets where regulatory requirements and labor costs can vary widely. Contract manufacturing transfers these operational responsibilities to the contract manufacturer. This arrangement allows foreign companies to avoid the continuous financial drain associated with running a manufacturing plant, thereby facilitating expansion at a lower cost. By reducing operational expenses, companies can enhance their profitability and allocate more resources towards strategic initiatives.
3. Mitigating Risks
Investing in a manufacturing facility in a foreign market carries inherent risks. These include regulatory uncertainty, geopolitical instability, and fluctuations in market demand. Such risks can jeopardize the return on investment and create financial instability. Contract manufacturing offers a solution by providing greater flexibility and agility. Companies can adapt to changing market conditions without being tied down by long-term capital investments. This flexibility allows them to respond swiftly to regulatory changes, economic shifts, and consumer preferences, thereby mitigating risks and enhancing their resilience.
4. Access to Expertise
Partnering with contract manufacturers allows foreign companies to leverage the expertise of established manufacturers without having to invest in building their own team of experts. Contract manufacturers typically have a wealth of experience and specialized knowledge in production processes, quality control, and supply chain management. By utilizing the skills and capabilities of these experts, foreign companies can improve product quality and accelerate time-to-market. This not only saves on capital expenditure but also ensures that products meet high standards of quality and compliance, enhancing the company’s reputation and competitiveness.
5. Flexibility in Production
Market demand is often unpredictable, influenced by factors such as consumer preferences, seasonal variations, and economic cycles. These fluctuations can impact production requirements, making it challenging for companies with their own manufacturing facilities to adjust quickly. Contract manufacturing offers the flexibility to scale production volumes up or down according to demand. This adaptability ensures that companies are not constrained by the capacity limitations of their own facilities, allowing them to meet market demand efficiently. By adjusting production based on real-time market conditions, companies can optimize their inventory levels, reduce waste, and improve overall operational efficiency.
Conclusion
Contract manufacturing is an effective strategy for saving fixed capital investment. By minimizing capital expenditure, reducing operational costs, mitigating risks, accessing specialized expertise, and offering flexibility in production, contract manufacturing enables foreign companies to focus on their core business activities and achieve their strategic objectives. This approach not only conserves financial resources but also enhances operational efficiency, product quality, and market responsiveness, making it an attractive option for businesses looking to expand and thrive in competitive markets.
Partnering with a reliable contract manufacturer like KredTrade can unlock these benefits, providing a robust foundation for growth and success in the dynamic global market.